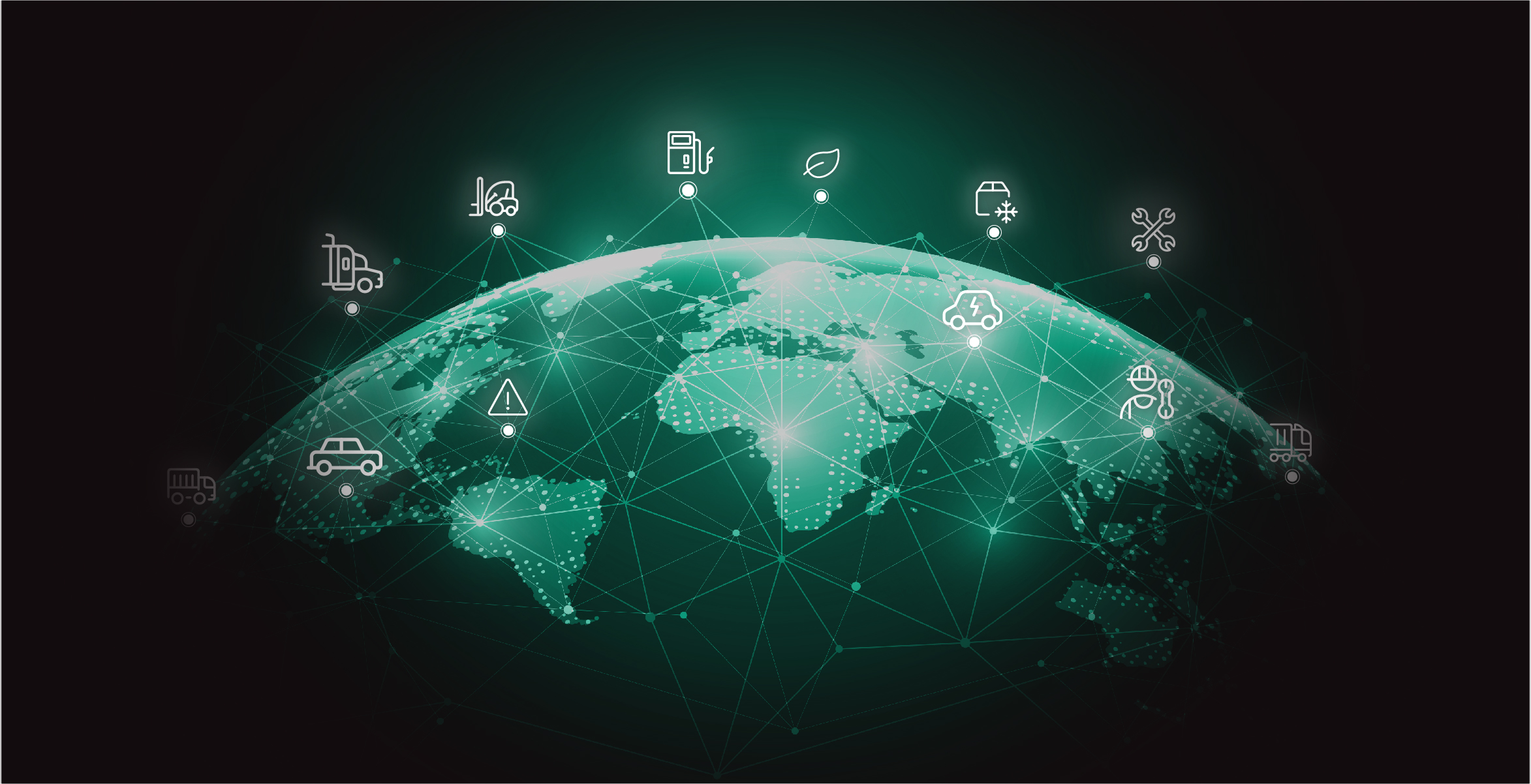
[help]
VisionAI On-Road – Eyes on the Road Hands on the Wheel
Powerfleet’s Vision AI offers an AI-driven video safety solution that enhances driver and asset protection by detecting and notifying operators and drivers of risky driving behaviours.
Powerfleet® removed risk factors and applied enforceable safety
measures for a large food manufacturing company. Each location
received technologically advanced and easily implemented processes
for worker safety and vehicle tracking. Powerfleet®’s advanced telematics digitize tracking, enabling management at any location
to monitor vehicle use and employee habits. This eliminated guesswork, provided accountability and created a new system of checks and
balances for measurable results. The company saw results in terms of a 70% decrease in accidents, an 80% decrease in damages and several hundred thousand dollars in cost savings.
Situation
Powerfleet®’s advanced telematics digitize tracking, enabling management at any location to monitor vehicle use and employee habits. This eliminated guesswork, provided accountability and created a new system of checks and balances for measurable results.
The company saw results in terms of a 70% decrease in accidents, an 80% decrease in damages and several hundred thousand dollars in cost savings.
Task
Improvements were required in the following areas:
The company has a fleet of over 150 industrial trucks, which include motorized walkie-rider pallet jacks, reach trucks and sit-down counterbalance forklifts. They required immediate help with monitoring personnel and reducing safety threats.
Action
Powerfleet® is an expert in streamlining safety operations. The intelligent designs and systems improvement transformed this company’s operations, drastically reducing risk and improving safety. The company needed a wireless telematics system designed for industrial trucks. Powerfleet® put into place:
Based on pricing, reliability and overall value, this company selected Powerfleet® as the best option on the market to implement these systems.
Powerfleet®’s services provide OEM-independent solutions over a long period of time. They implemented the above systems, many of which are patented and unique to Powerfleet® as a company.
Powerfleet’s® implementation of software and hardware happened over the course of just a few weeks.
Powerfleet Took These Steps
Results
The client reports that Powerfleet® achieved the following results:
Additional outcomes eliminated badge-sharing among employees, created a “driver break” function to prevent unauthorized vehicle use and actioned an alert system for any maintenance issues or safety violations. The combined efforts had the additional results of:
Conclusion
Powerfleet®’s patented, industrial management technology transforms drivers’ situational awareness and reduces the number of accidents. It streamlines real-time communication and eliminates false alarms. Managers can respond quickly to accidents or safety events and create proactive measures to avoid costly issues. With integrated systems, meaningful data can be collected that informs best practice and better processes for the companies who use Powerfleet®’s software and hardware.
Powerfleet transforms the way organizations manage mobile business assets — like forklifts, cargo trailers, and connected cars. Our technologies control, track, analyze, and optimize hundreds of thousands of these assets all over the world. We help organizations be safer, improve efficiency, and cut costs.
Powerfleet® provided operational support, telematics and software
systems that transformed safety and improved revenue for a global
manufacturer. Powerfleet®’s forklift fleet management and analytics provide real-time data. This protects workers by remote vehicle monitoring, maintenance alerts and reduction of costs associated with lift truck accidents. Additionally, telematics contribute to proper material handling, creating a more cost-effective and risk-free environment for large-scale production. The company deployed Powerfleet’s software and hardware at five manufacturing plants with over 800 vehicles of varying types. They achieved millions of dollars in labor costs, 80% forklift accident reduction and 100% personnel safety compliance.
Situation
A global manufacturer needed solutions for heavy manufacturing processes. These occurred in five separate locations and used about 800 vehicles, including lift trucks, tow tractors and man lifts. They needed solutions that would improve safety in material handling operations, protect workers and reduce costs.
Task
The customer needed a system that would ensure OSHA compliance,
streamline communication and improve safety. Their primary goals were:
The company had (or has) 800 material handling equipment (MHE) vehicles in five locations. Each goal would have to be achieved in different environments, with different leadership and employees.
Action
Powerfleet® sets the standard in the industry for safety enforcement and efficiency for industrial vehicles and access control systems. Powerfleet® put into place:
Powerfleet®’s systems comply with corporate and government safety
regulations. All vehicles are digitally monitored both for location and status. Drivers are accountable in their operation, which promotes safer practices.
Powerfleet Took These Steps
Powerfleet’s installed software and hardware with minimal disruption to
operations in each facility. These included:
Additionally, leadership at the company began to use Powerfleet® IQ™ Analytics to assess their systems. This source of information provided both a baseline and immediately identifiable areas for improvement which provided immediate action items for improvement in low-performing sites. They were able to reduce waste and improve operations for maximum utilization at all times.
Results
The client reports that Powerfleet® achieved the following results:
The client reports that, “Very quickly, we were able to reduce forklift damage costs over 80% and get our pre-shift checks into 100% compliance.”
Conclusion
Powerfleet®’s telematics and Powerfleet® IQ™ Analytics provided a novel source of data and improvement plans for this global manufacturer. Across numerous facilities and on hundreds of different vehicles, all of these
systems vastly improved function and streamlined processes. Operations
and personnel were improved through Powerfleet®’s sophisticated,
innovative, digital tools.
Powerfleet transforms the way organizations manage mobile business assets — like forklifts, cargo trailers, and connected cars. Our technologies control, track, analyze, and optimize hundreds of thousands of these assets all over the world. We help organizations be safer, improve efficiency, and cut costs.
Powerfleet® reduced risk and increased revenue for the customer in this case study. Innovators at Powerfleet® undertook this project for a client in automotive manufacturing by providing fleet management and analytics for five manufacturing plants. These plants had an industrial truck fleet of over 800 vehicles, including lift trucks, tow tractors and man-lifts. The work performed saved the company over $2 million a year and continues to pay off in terms of efficiency and effectiveness.
Situation
A leader in global automaking found themselves in need of improved safety measures and material handling operations. The company adheres to the highest safety standards but their ongoing self-monitoring processes indicated a need for improvement. The need extended to personnel training, systems implementation, systems management, authorization processes and equipment use monitoring.
Task
This automaker needed safety and operational improvement for two reasons:
The company is known for safety technologies. The workforce in new safety systems included people working on forklifts and other MHE. Powerfleet’s objective was to improve control over industrial truck safety policies. The work and systems implemented by Powerfleet® addressed the client’s acute and long-term needs.
Action
Powerfleet® excels in logistics, industrial telematics and vehicles. Two of Powerfleet’s tools were used in this case:
These tools provided a dual-action solution to the automaking company’s safety needs.
Powerfleet Took These Steps
Results
Powerfleet saved this client millions of dollars and put a system in place that will benefit their business in numerous ways. Results of this work included:
Conclusion
Powerfleet® is uniquely equipped to assist companies in numerous facets of this industry. Our cutting-edge technology and applied practices can improve systems and optimize efficiency. In this case, our work ensured the safety of employees and reduced costs.
Powerfleet transforms the way organizations manage mobile business assets — like forklifts, cargo trailers, and connected cars. Our technologies control, track, analyze, and optimize hundreds of thousands of these assets all over the world. We help organizations be safer, improve efficiency, and cut costs.
[help]
Powerfleet’s Vision AI offers an AI-driven video safety solution that enhances driver and asset protection by detecting and notifying operators and drivers of risky driving behaviours.
[help]
Safety has consistently improved after implementing the Powerfleet In-Warehouse solutions. Using Powerfleet’s Enterprise Dashboards, this food and beverage customer was able to change the way it measured and balanced productivity (pallets moved)
safely (forklift collisions) and efficiency (active time on equipment vs. paid time).
[help]
Powerfleet’s AI-Powered Solutions Power Safety and Sustainability for The Miller Group’s Diverse Fleet Operations.
[help]
Powerfleet and DrabPol SP: Driving Safer Roads and Smarter Fleet Solutions in Poland and Ukraine
[help]
Learn more About How Powerfleet EasyCheck Enhances Fleet Safety, compliance and Uptime.
[help]
Powerfleet’s Pedestrian Proximity Detection uses intelligent cameras to identify people and vehicles in industrial environments, helping to prevent accidents before they happen. The system provides alerts without requiring special apparel and delivers actionable analytics to enhance workplace safety.
[help]
In this testimonial video, learn how our integrated system enables real-time visibility of forklift activities, enhances safety protocols, and provides actionable data for better operational decision-making and resource planning
[help]
Unity is Powerfleet’s robust end-to-end AIoT data highway. It unifies operations to transform business performance across key market drivers, keeping businesses operating safely, compliantly, and sustainably.
[help]
Powerfleet Solutions Drive Swans Travel Limited’s Commitment to Safer Roads and Reduced Emissions.
[help]
As a construction dealer, you play a pivotal role within this dynamic industry. Elevate Your Construction Dealership with Enhanced Operational Performance